Case Study: Helping a Nationwide Retailer Reduce Plastic Waste
Pounds of material recycled that would have been landfilled.
%
Reduction in cost to source high quality post-consumer recycled feedstock.
Truckloads of used car seats managed in less than a couple of weeks.
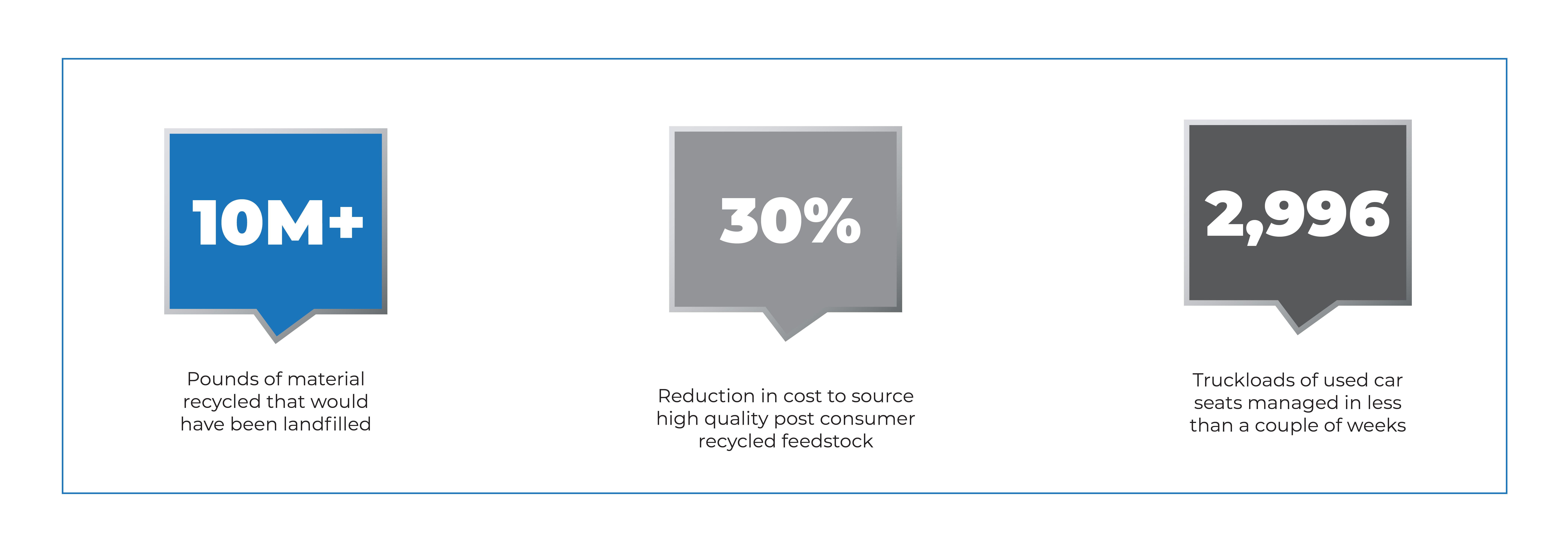
How 1GNITE created a nationwide network to manage hard to recycle material in a matter of weeks and helped a nationwide retailer reduce plastic waste.
THE ISSUES
A nationwide retailers with over 4,000 stores identified plastics as the largest recyclable commodity that affects the products sold in their stores and used in their operations. The multinational corporation was committed to reduce plastic it’s operation sends to the landfill. During a promotional event, the retailer allowed consumers to bring back old child safety seats to be recycled for free and provided a coupon for instant in store purchase. The volume collected in one week exceeded 1M, or 5 times expectations, overwhelming the current recycling program in place. How 1GNITE created a nationwide network to manage hard to recycle material in a matter of weeks and helped a nationwide retailer reduce plastic waste.
THE SOLUTIONS
- 1GNITE pulled from its extensive network of transporters, consolidators, recyclers and processors and created a nationwide child safety seat recycling program capable of handling millions of child safety seats.
- 1GNITE worked with car seat manufacturers to establish recycled plastic resin specifications that would allow the post-consumer recycled material to be easily used as a raw material to make other baby items.
- 1GNITE created a closed loop manufacturing process that provided manufacturers with a ready to use feedstock.
1GNITE’s unique creativity and resourcefulness helped us recycle more than one million child safety seats that were clogging our return centers. They completed in a few weeks what other companies said would require a year.
1GNITE’s unique creativity and resourcefulness helped us recycle more than one million child safety seats that were clogging our return centers. They completed in a few weeks what other companies said would require a year.
THE RESULTS
A nationwide program to cost-effectively recycle a notoriously difficult to recycle consumer good and a blueprint to a first of its kind closed loop manufacturing process.
THE IMPACTS
- 1GNITE created a national program to cost-effectively recycle child safety seats, which are very difficult to recycled.
- The new program collected, transported, recycled and processed over 10M of pounds of materials in a matter of weeks, eliminating a stockpile of returned car seats that no other company would touch.
- The closed loop manufacturing program generated a high quality feedstock of raw material that was about 30% cheaper than virgin material.
- The retailer ran a very successful return program that boosted consumer loyalty while ensuring that the returned material was safely recycled.
-
Liquidation: How Retailers Retain Value for Planned and Unplanned Events
-
3 Easy Steps To Align Emergency Liquidation and Recycling
-
Liquidation company: how to pick the right one
-
4 Proven Steps to Successfully Implement an Internal Marketplace
-
5 Benefits of an Internal Marketplace You Must Know
-
Warehouse Cleanout: How To Decide What Stays and What Goes?